All Vahterus heat exchangers are designed with the required design codes such as. Of Process Equipment Design PLATE HEAT EXCHANGER SELECTION SIZING AND TROUBLESHOOTING ENGINEERING DESIGN GUIDELINES Page 6 of 97 Rev.
Plate Heat Exchangers Components Types Applications And Advantages
ASME units require ASME relief devices per UG-125 of ASME Code Section VIII Div.
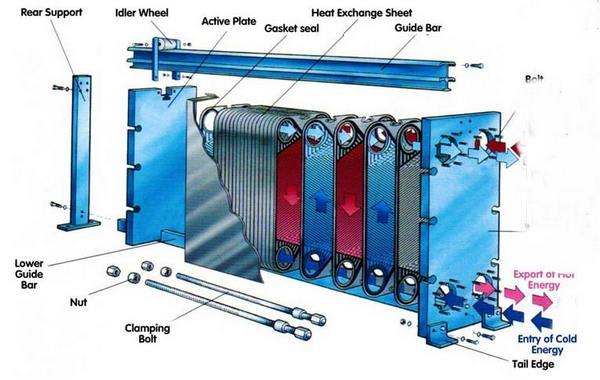
. Thanks Ankur for the answer. - 0 40 bar g Condensers convert steam into liquid. Typical velocities in plate heat exchangers for waterlike fluids in turbulent flow are 03-09 ms but true velocities in certain regions will be higher by a factor of up to 4 due.
It is considered that no heat loss to surroundings. Using the boundary condition equations 7 and 8 for all the channels of the PHE under investigation the equations presented. H for plate heat exchanger is often in between 2 to 7 kWm 2 K -1.
Anyone knows other codes standards of plate and frame heat exchanger used for downstream servicesrather than API 662 please help me. 1 Preventing Excessive Pressure. T hi inlet temperature of hot fluid K It is then possible to approximate the size of the heat exchanger by estimating the overall heat transfer coefficient H.
The heat exchanger during maintenance. A pressure vessel design code alone cannot be expected to cover all the special features of heat exchangers. Guidelines for the design materials fabrication inspection testing and preparation for shipment of air-cooled heat exchangers for use in the petroleum and natural gas industries.
Similar logic applies to different pressure vessel. H overall heat exchange coefficient kWm 2 K-1. AHRI 400-2001 with Addenda 1 and 2.
A universally accepted code for shell and tube exchangers is TEMA 1988 which although designed to supplement ASME VIII can be used in conjunction. To give guidance and protection to designers manufacturers and purchasers a supplementary code is desirable. Liquid to Liquid Heat Exchangers was developed for plate and frame heat exchangers because many applications in commercial HVAC systems were designed with very close.
But its the code for Plate heat exchanger used for offshore service. October 1 2012 - DS. For a given heat exchanger de ned by heat exchanger type a range of variables de ning the geometry of the heat exchangers selected heat transfer correlations and selected pressure drop correlation the exchanger performance is evaluated.
C 8 z 1 8 z 2 8 z 8 8 e λ 8 η. By geometry and heat transfer analysis the total number of plates the actual with fouled surface and required heat duty are found as 105 plates 263 x 107 W and 232 x 107 W respectively. A plate heat exchanger is used to transfer heat energy from one fluid to another.
Plate Heat Exchangers for General Refinery Services Part IPlate-and-Frame Heat Exchangers. This means that the condensing liquid creates a film where the steam condenses. 4214 Tube-Side Heat Transfer Coefficient The heat transfer coefficient for the tube-side is expressed as follows.
H for plate heat exchanger is often in between 2 to 7 kWm 2 K -1. θ η c 1 z 1 1 z 2 1 z 8 1 e λ 1 η c 2 z 1 2 z 2 2 z 8 2 e λ 2 η. Steam condenses on the surface which is colder than the saturation temperature of the steam.
Due to this unique construction Vahterus Plate Shell Heat Exchangers can meet very demanding design conditions. Design Pressure and maximum working temperatures shall be in accordance with project plans. 3Once the plate pack is inserted the tie bars are put in place.
The plate heat exchanger frame and connections are assembled and the plates start to be put in place. Plate Heat Exchanger Design. Ive searched around and found BP GS 126-5 Anyone needs this code PM me.
MAWP of other pressure retaining parts will govern the design. ISO 122112012 specifies requirements and gives recommendations for the mechanical design materials selection fabrication inspection testing and preparation for shipment of spiral plate heat exchangers for the petroleum petrochemical and natural gas industries. Typically a plate heat exchanger will consist of several parallel plates positioned above each other thus creating a passage in which the fluid can flow between.
The Plate Frame Heat Exchanger shall be designed and tested to the latest ASME Code Sect. TEMA designations refer to portions of the unit that make up the complete heat exchanger. The codes cover all aspects of the construction of heat exchangers except the types of service loads other than pressure and the thermal design.
Employing a xed heat exchanger geometry allows the performance of a given heat exchanger to be evaluated as. However plate heat exchangers which can operate at pressures up to 25 bar are available. From -270C to 750C.
Design temperatures and pressures. K 47 i t t t d h Nu where is the Nusselt number for the tube-side fluid which is found by using Eqs. The figure below is helpful in visualizing each segment.
02 Rev 02 Feb 2020 These design guideline are believed to be as accurate as possible but are very general and not for specific design cases. In a plate heat exchanger condensing is film condensing. Air-Cooled Heat Exchangers for General Refinery Service.
Fizza453 Mechanical OP 20 Mar 17 1214. The goal of the project is to understand the characteristics and design of a plate heat exchanger. The normal maximum operating pressure for a plate heat exchanger is generally 16 bar for ASME-code units.
In an effort to study and optimize the design of a plate heat exchanger comprising of corrugated walls with herringbone design a CFD code is employed. Full vacuum to 150 bar. TEMA Type BEM would have the B representing the front head the E the core or middle section and M representing the rear head designs.
The manufacturer or his agent must be registered with the National Board. Each plate in the plate pack is individually inserted into the frame in the correct order as per the final duty design. Under ASME rules if the operating pressure is higher than 15 psig then the heat exchanger is considered a pressure vessel and the pressure-vessel design code ASME section VIII Div.
64 DESIGN PRESSURE Operating a plate heat exchanger above its. - 0 400C. λ thermal conductivity η viscosity c p specific heat subscription w wail.
1 or 2 applies. TYPICAL PLATE HEAT EXCHANGER ASSEMBLY PROCEDURE. I found the Code Case 2766 it does not require any design calculations or proof testing for establishing the MAWP for gasketed plate packs provided all 6 conditions of CC2766 are met.
These fluids never encounter each other due to being separated by the heat exchanger. 44 and 46 k is the thermal conductivity of the tube-side fluid and is the tube inside diameter.
Plate Heat Exchanger Engineering
Plate Heat Exchangers Layout The Piping Engineering World
25 Plate Heat Exchanger Configuration Download Scientific Diagram
How Plate Heat Exchangers Work The Engineering Mindset
Brazed Plate Heat Exchanger 40 Plates 5 X12 1 1 4 Mpt 530 000 Btu Heating Systems Heat Exchanger Domestic Hot Water
Ab Brazed Plate Heat Exchanger 20 Plates 5 X12 1 1 4 Mpt
Basic Structure Of Plate Heat Exchanger Phe Source Reproduced With Download Scientific Diagram
0 comments
Post a Comment